Home » Articles posted by Nicole Preston
Author Archives: Nicole Preston
Insulation Removal – A Demanding Project That Requires Specified Tools and Expertise
Insulation removal is a demanding project, requiring specialized tools and expertise. Insulation Removal Perth services can bring a level of efficiency and safety to the task that DIY simply cannot match.
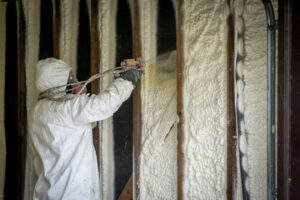
Moisture, pest infestation, and deteriorating materials often necessitate insulation removal in homes. Fortunately, replacing old insulation can make your home more comfortable and energy-efficient.
Insulation is a vital home component that contributes to health, savings, and resale value. However, it can degrade over time due to age, moisture, and pest infestation, requiring removal or replacement. A proper insulation removal process includes assessment and inspection to identify damage, contamination, and poor performance and prepare the attic or walls for new materials.
In the attic, old and contaminated insulation can harbor mold, rodents, and other pests that contribute to unhealthy indoor air. This material can also be a breeding ground for mildew, which can lead to moisture issues that can damage the structure of your house. Insulation removal clears out contaminates and enhances indoor air quality, providing a safer environment for household members with respiratory conditions or allergies.
Moisture can penetrate wall and crawl space insulation through a variety of means, including heavy rain or unprotected shingles. Inadequate moisture control can cause insulation to deteriorate or even rot, leading to water leaks and a host of problems.
Insufficient or contaminated insulation leads to energy inefficiency, forcing heating and cooling systems to work harder to stabilize indoor temperatures. Replacing it with high R-value insulation significantly improves home energy efficiency and reduces heating and cooling costs.
During the assessment and inspection phase, professionals examine your attic or other areas for visible signs of insulation degradation. If you notice a sudden increase in energy bills or the presence of moisture, odors, or pests, this is a good indication that your existing insulation needs to be removed and replaced.
The assessment and inspection process typically involves turning off the power to the attic or other areas where the insulation will be removed. This prevents accidental damage to electrical systems and ensures workers’ safety. Insulation removal specialists are also trained to identify potential hazards like asbestos and cadmium in order to take the necessary precautions.
The next step in the insulation removal process is removing and decontaminating existing materials. This is particularly important in crawl spaces or other tight spaces, where existing insulation may be exposed to moisture and pests. It is also important to ensure that the area is properly sanitized and prepared for new insulation. This is critical for ensuring that new materials are installed effectively and that the entire attic is protected from pests and moisture, preventing future issues and maintaining the energy efficiency of your home.
Preparation
Insulation often needs to be removed or replaced due to damage, aging, or the need for an upgrade to energy efficiency. While navigating the process can seem daunting, proper preparation can make it easier for any homeowner to complete this project safely and effectively.
Before beginning insulation removal, it’s important to thoroughly assess the area and make sure that the current material is in good condition. Look for signs of mold or water damage, and check that beams and joists are intact. It’s also an ideal opportunity to perform any energy upgrades that can improve comfort and help save on utility bills.
Preparing the workspace for insulation removal can also reduce the risk of accidents and ensure a more efficient process. Clearing the area and removing any unnecessary items can help create a workspace that’s easier to navigate, while plastic sheeting can be used to isolate areas and prevent dust from spreading. Using fans to maintain adequate ventilation is crucial as well. Proper PPE should be worn at all times to protect against irritants like dirt, mold, and rodent droppings.
Before starting work, it’s also important to turn off and disconnect all power sources in the attic. Working around live wires can pose a safety risk and may cause serious damage to home electrical systems. Taking the time to turn off and disconnect the power will help to prevent electrical shocks or fires, minimizing the potential for injury or damage to the home’s structure.
Loose-fill insulation is usually a bit more challenging to remove than fiberglass batts or foam board, but professionals can utilize equipment to remove the material quickly and efficiently. It’s advisable to use heavy-duty waste bags and seal them tightly to prevent loose fibers from escaping. Organizing and labeling the bags will help sanitation workers identify the contents when disposing of them. It’s also a good idea to rent a dumpster to streamline the process and avoid waste management issues.
Certain types of insulation can contain hazardous materials, such as asbestos or lead paint, which require special precautions when removing and replacing. Professionals can use specialized equipment to test for the presence of these materials, and decontamination and cleaning procedures can be performed as needed.
Removal
Insulation removal is the process of safely and systematically extracting insulation material from walls, ceilings, floors, and other areas. It can be carried out for several reasons, including replacing aging or damaged insulation, addressing pest infestations, and improving energy efficiency.
The type of insulation that requires removal will determine the proper methods used to carry out this task. For example, spray foam and cellulose insulation require different approaches than fiberglass insulation. A professional should be able to provide recommendations and advice regarding the best method for removing each specific insulation type. Prior to beginning the process, it’s important that the work area is properly prepared. This includes clearing out attic spaces and ensuring that any valuables or personal belongings are moved away from the area. It’s also a good idea to wear appropriate personal protective equipment, such as a respirator and mask to prevent inhalation of insulation dust and other contaminants. Gloves, goggles, and disposable coveralls are also recommended to protect skin and eyes from irritants.
Before the insulation can be removed, it’s important to ensure that any electrical wires or junction boxes located within the attic space are disconnected and sealed. This reduces the risk of electrical shock and fires during the process.
Once the area is free of all obstructions, the insulation can be carefully removed using a variety of tools and techniques. For instance, blown insulation can be vacuumed up with a specialized equipment that uses high-pressure jets of air to remove the materials without damaging other building elements. In some cases, loose-fill insulation may be loosened with a shovel or a rake and scooped into bags for disposal.
Using the right tools and technique is critical to ensuring that all contaminants are safely and efficiently removed from the work area. This ensures that the work is completed in a timely manner, with minimal disruption to the surrounding environment and complying with all environmental and safety regulations.
Removing and replacing old insulation is a necessary home maintenance activity that should be addressed sooner rather than later. As time passes, older forms of insulation will lose their effectiveness and may even degrade. A professional insulation contractor will have the equipment and knowledge necessary to complete the task in a safe and effective manner. Moreover, installing new insulation will improve a property’s energy efficiency and raise its resale value for potential buyers.
Disposal
Insulation removal is a messy job that requires specialized equipment to properly execute. The first step is to identify the type of insulation in a building and prepare for the removal process. This may involve ensuring that personal protective gear is available, such as masks, safety goggles, and respirators to prevent contact and inhalation of harmful materials. It also involves setting up a work area that is sealed off from other areas of the home and ensuring all tools necessary for the project are present. For instance, a vacuum with a specialized attachment is ideal for loose-fill insulation, while a rake can help in transferring the material to waste bags.
Once the attic is cleared of old insulation, it’s important to perform a thorough inspection of the space to ensure all hazardous materials have been removed. This includes checking for rodent droppings and identifying any signs of mold growth, which can cause health problems. It’s also important to verify that all areas have been thoroughly cleaned and decontaminated, especially if the house has suffered any damage from a fire or flood. In such cases, the old insulation may contain asbestos and require special treatment.
It’s vital to ensure all old insulation is disposed of in accordance with local regulations. This is a crucial aspect of the removal process that many homeowners overlook, but doing so can help to prevent environmental contamination and protect the community. Professional insulation removal services are equipped to handle this task, and can often provide additional benefits like rodent proofing and attic cleaning services.
In addition to ensuring the correct disposal of all materials, it’s also recommended that the homeowner check with local authorities for guidelines regarding recycling facilities that accept insulation material. This will not only help to reduce the amount of waste, but can also save money by reducing disposal costs. In some cases, the recycled insulation can be used for other projects around the home, such as repurposing fiberglass batts or cellulose panels. This can make insulation removal a valuable investment for any home owner.